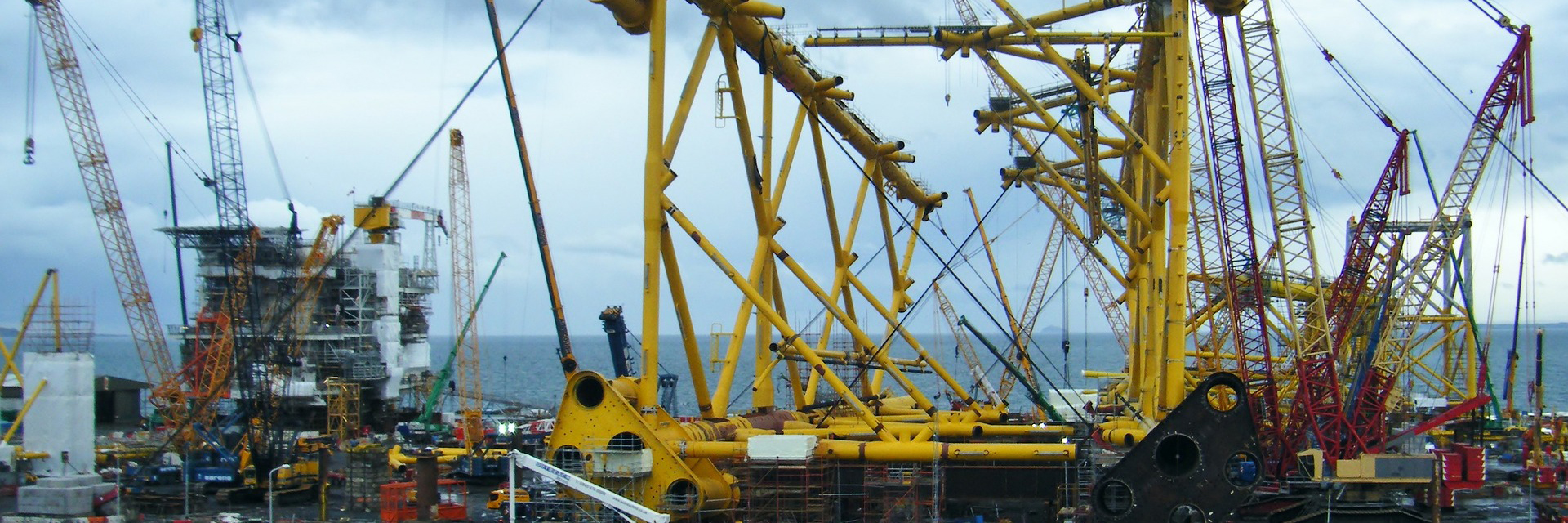
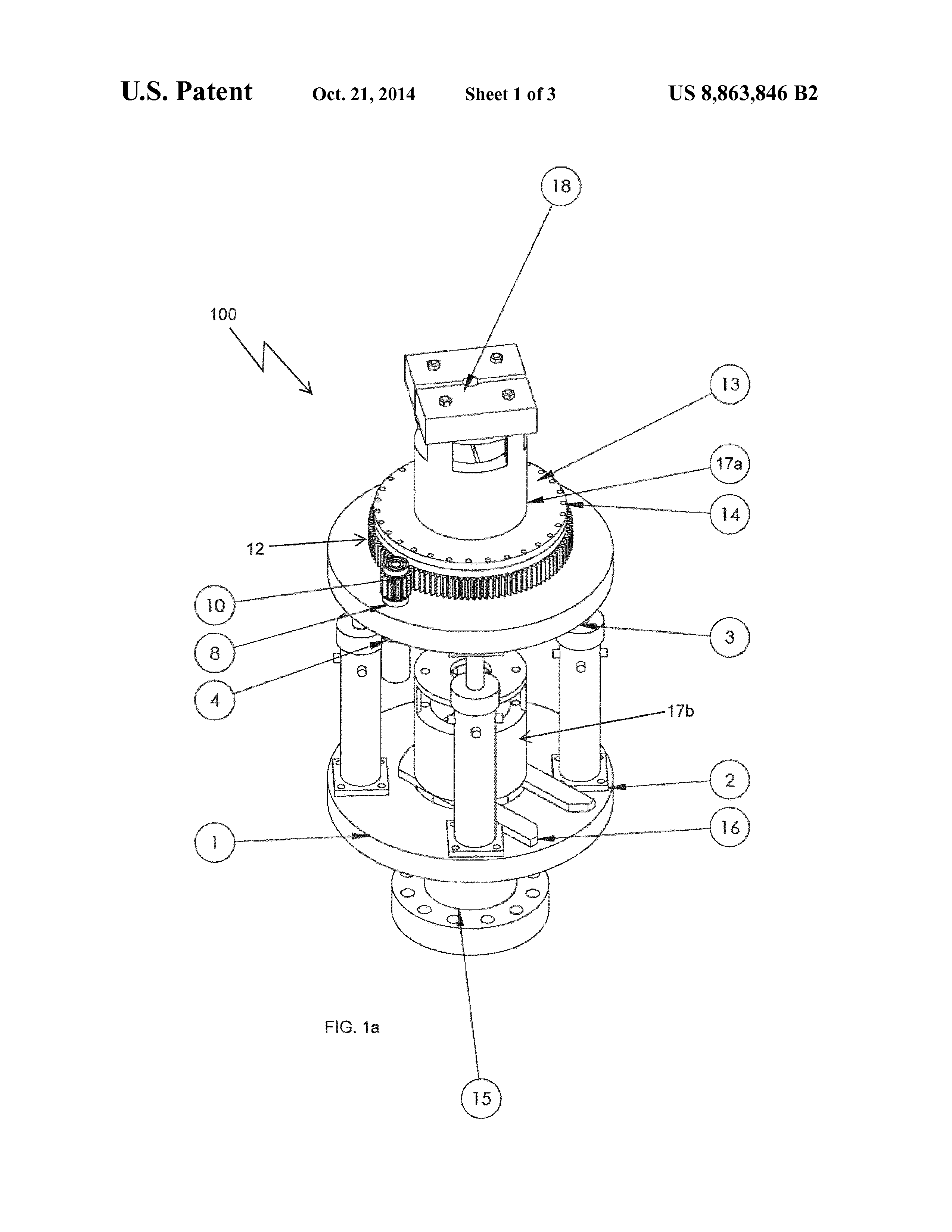
A jack system may provide subsea or surface operation. The jack system includes a top plate and a base plate with at least two pistons disposed between the base and top plate. The pistons are extendable to increase a separation distance between the base and top plate, and said pistons are retractable to decrease the separation distance between the base and top plate. The jack system also includes a bottom slip bowl assembly, a top slip bowl assembly, and rotary assembly. The top slip bowl and rotary assembly are rotatably coupled to the top plate wherein the rotary assembly and the top slip bowl assembly rotate relative to the top plate.
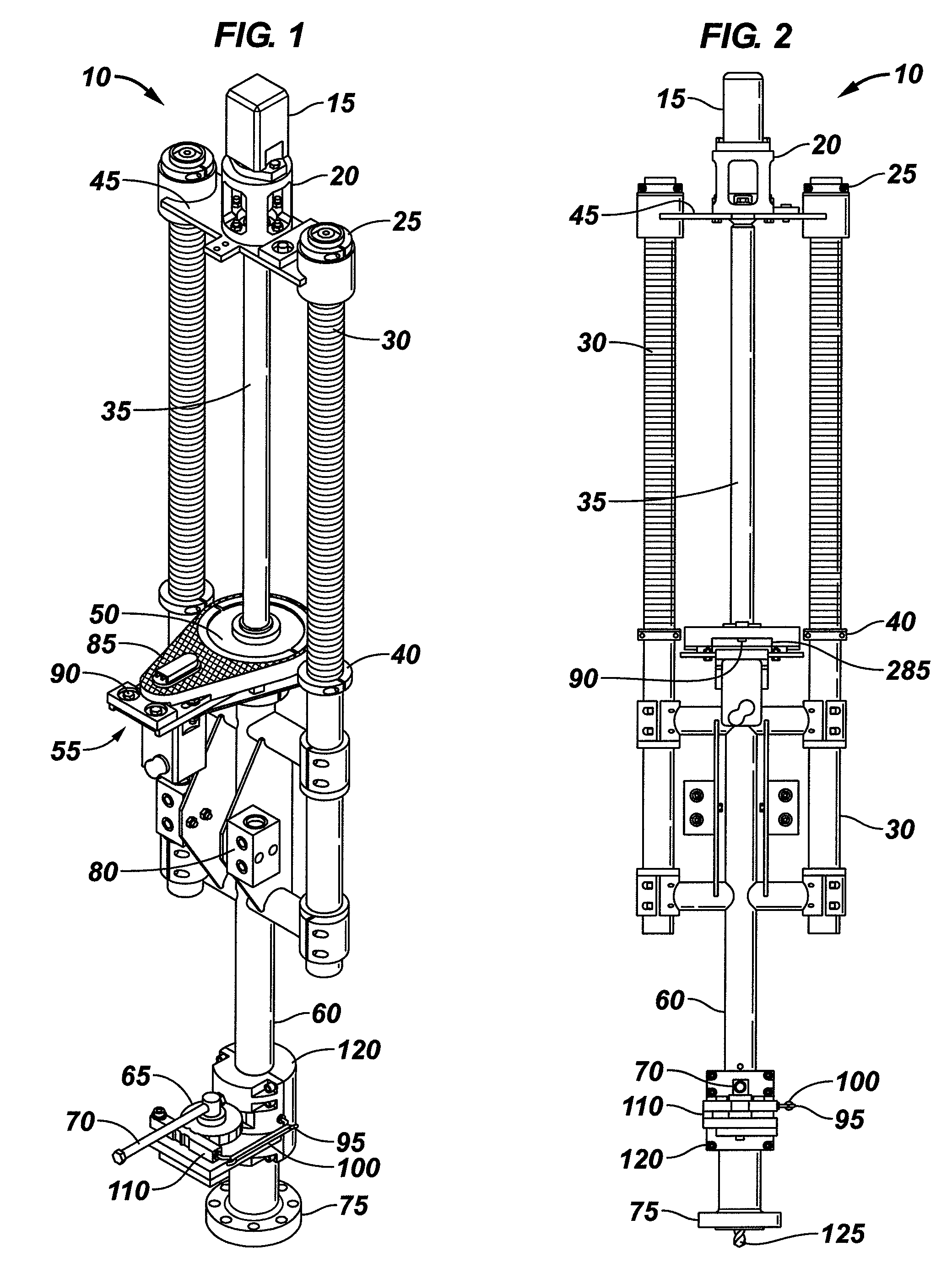
An assembly and method for tapping into a pressurized tubular that is adapted for use in a subsea environment via a diver or remotely operated vehicle. The assembly includes a tapping tool connectable to the tubular via a saddle connection
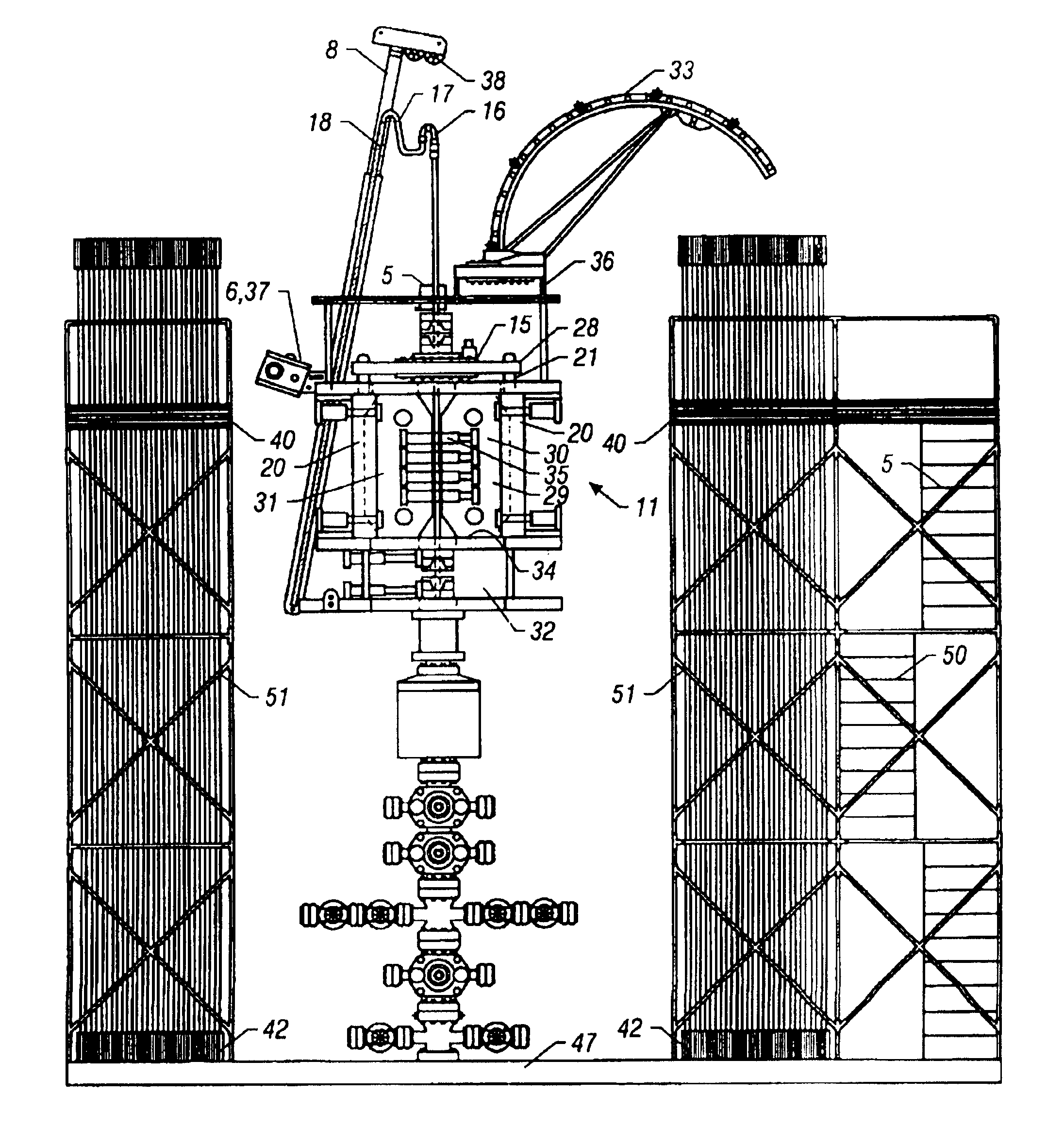
Method and apparatus for drilling, completion, well workovers and well control, combining an integrated lifting unit and a coiled tubing unit, the method and apparatus permit running jointed pipe and coil tubing in combination, and standing multiple joints of pipe near the unit. The invention combines a hydraulic pipe hoisting system, pipe handling systems and pipe racking containment apparatus. A hydraulic workover jack is combined with a multifunction injector head and a standpipe for fluid circulation. The invention may also include a rotary table for rotating pipe and/or a rotating power swivel to allow fluid circulation during pipe rotation. Also included are a gin pole, a winching system for jointed pipe, and a traveling head with traveling slips and stationary slips to allow pipe movement in the well. Hydraulic systems allow insertion and extraction of tools in a work string. The apparatus includes spoolable drill pipe including a connector, multi-section reel with core, connection to reel for fluid circulation, reel drive mechanism and a pipe pulling capability.
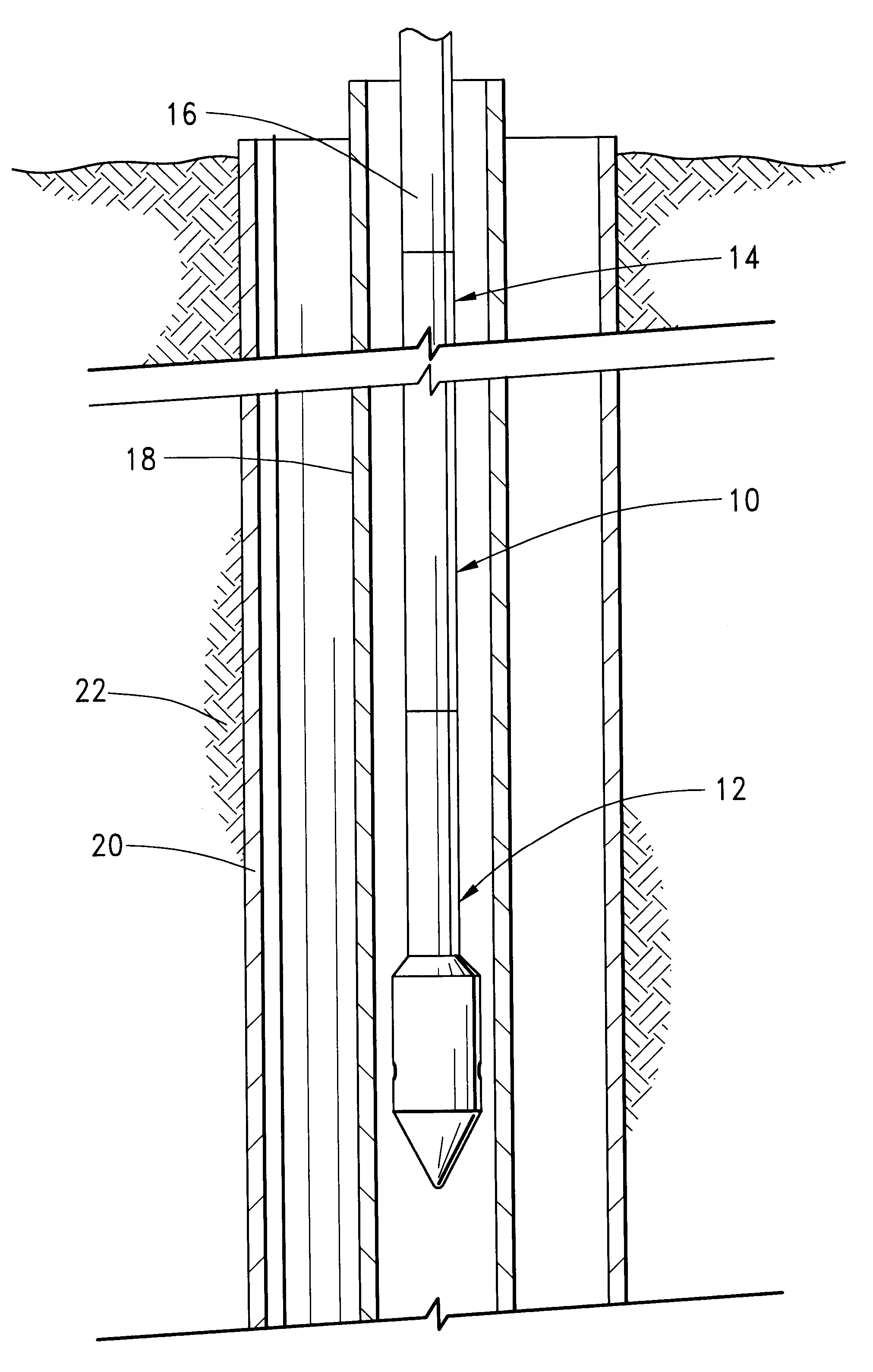
A fluid cutting tool and method for perforating or severing tubular members from inside. The tool is especially suited for use with a rotational drive system, such as a downhole motor, to separate downhole structures, such as stuck production tubing. The cutting tool preferably takes the form of an elongate metal body with an open first end connectable to the end of a downhole motor. The downhole end of the tool may be conical. A fluid conduit within the body of the tool communicates with the fluid channel in the downhole motor. Ports in the sides of the tool body direct jets of cutting fluid out the side of the tool. The tool attached to the motor is fed downhole until the tool is at the desired location in the well. Then the motor is operated to rotate the tool while cutting fluid is pumped through it. This causes the jets of fluid to be directed at the inner surface of the production tubing (or other tubular structure). This process is continued until the tubing is perforated or severed, as needed.
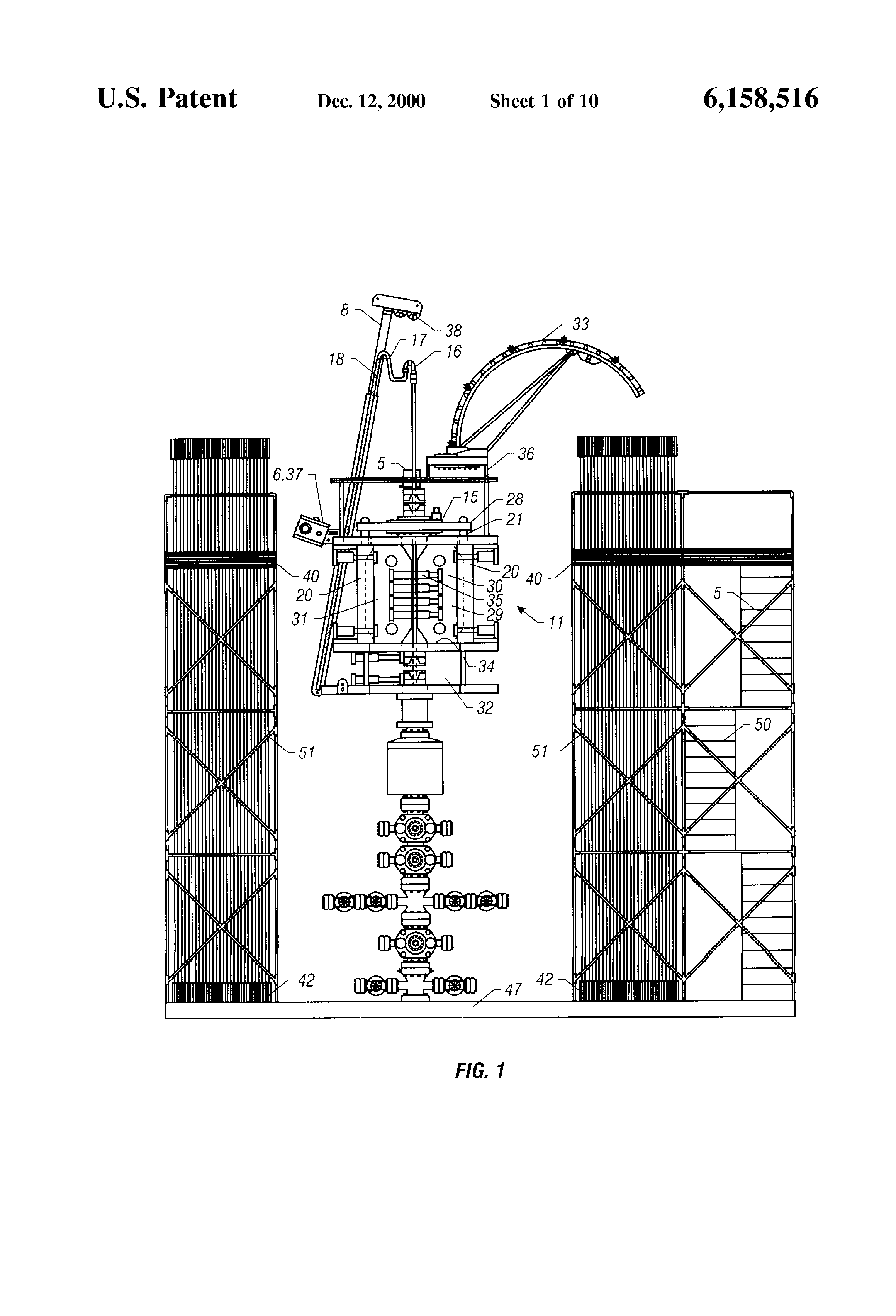
Method and apparatus for drilling, completion, well workovers and well control, combining an integrated lifting unit and a coiled tubing unit, the method and apparatus permit running jointed pipe and coil tubing in combination, and standing multiple joints of pipe near the unit. The invention combines a hydraulic pipe hoisting system, pipe handling systems and pipe racking containment apparatus. A hydraulic workover jack is combined with a multifunction injector head and a standpipe for fluid circulation. The invention may also include a rotary table for rotating pipe and/or a rotating power swivel to allow fluid circulation during pipe rotation. Also included are a gin pole, a winching system for jointed pipe, and a traveling head with traveling slips and stationary slips to allow pipe movement in the well. Hydraulic systems allow insertion and extraction of tools in a work string. The apparatus includes spoolable drill pipe including a connector, multi-section reel with core, connection to reel for fluid circulation, reel drive mechanism and a pipe pulling capability.
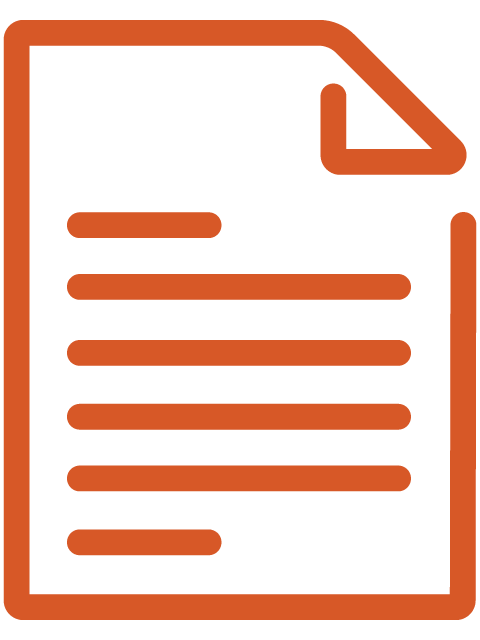
Patent pending.
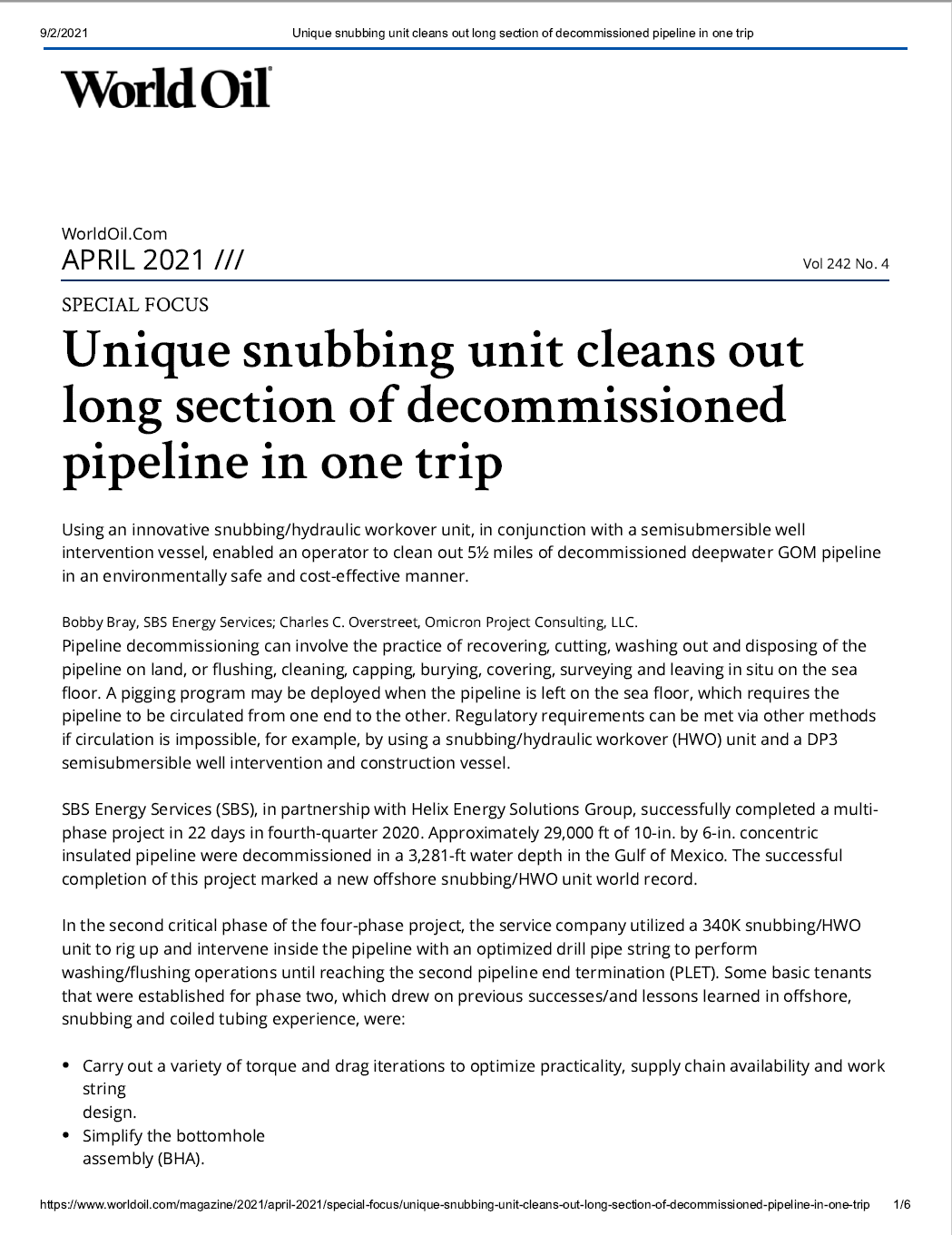
Introduction
Using an innovative snubbing/hydraulic workover unit, in conjunction with a semisubmersible well intervention vessel, enabled an operator to clean out 5 1/2 miles of decommissioned deepwater GOM pipeline in and environmentally safe and cost-effective manner.
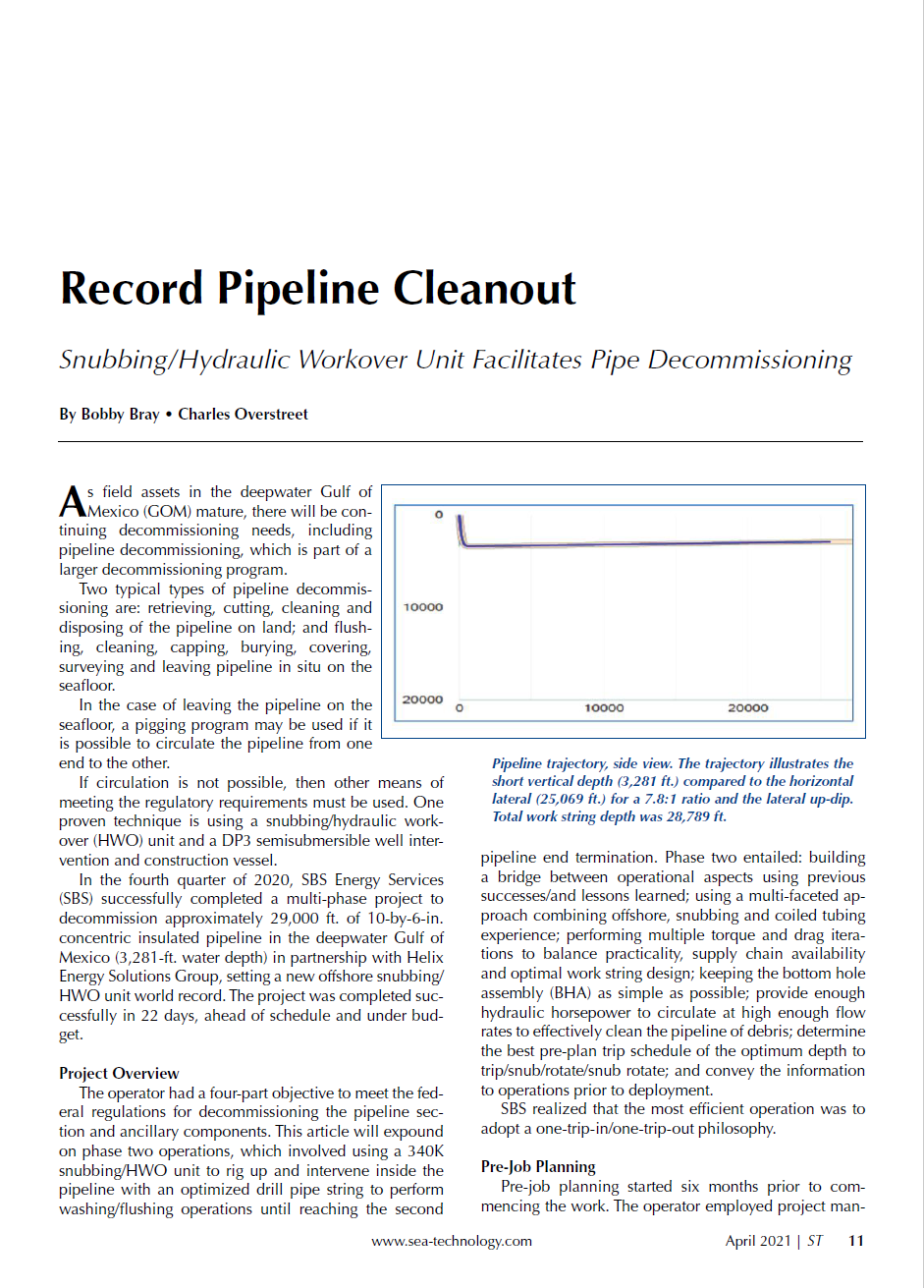
Introduction
As field assets in the deepwater Gulf of Mexico (GOM) mature, there will be continuing decommissioning needs, including pipeline decommissioning, which is part of a larger decommissioning program.
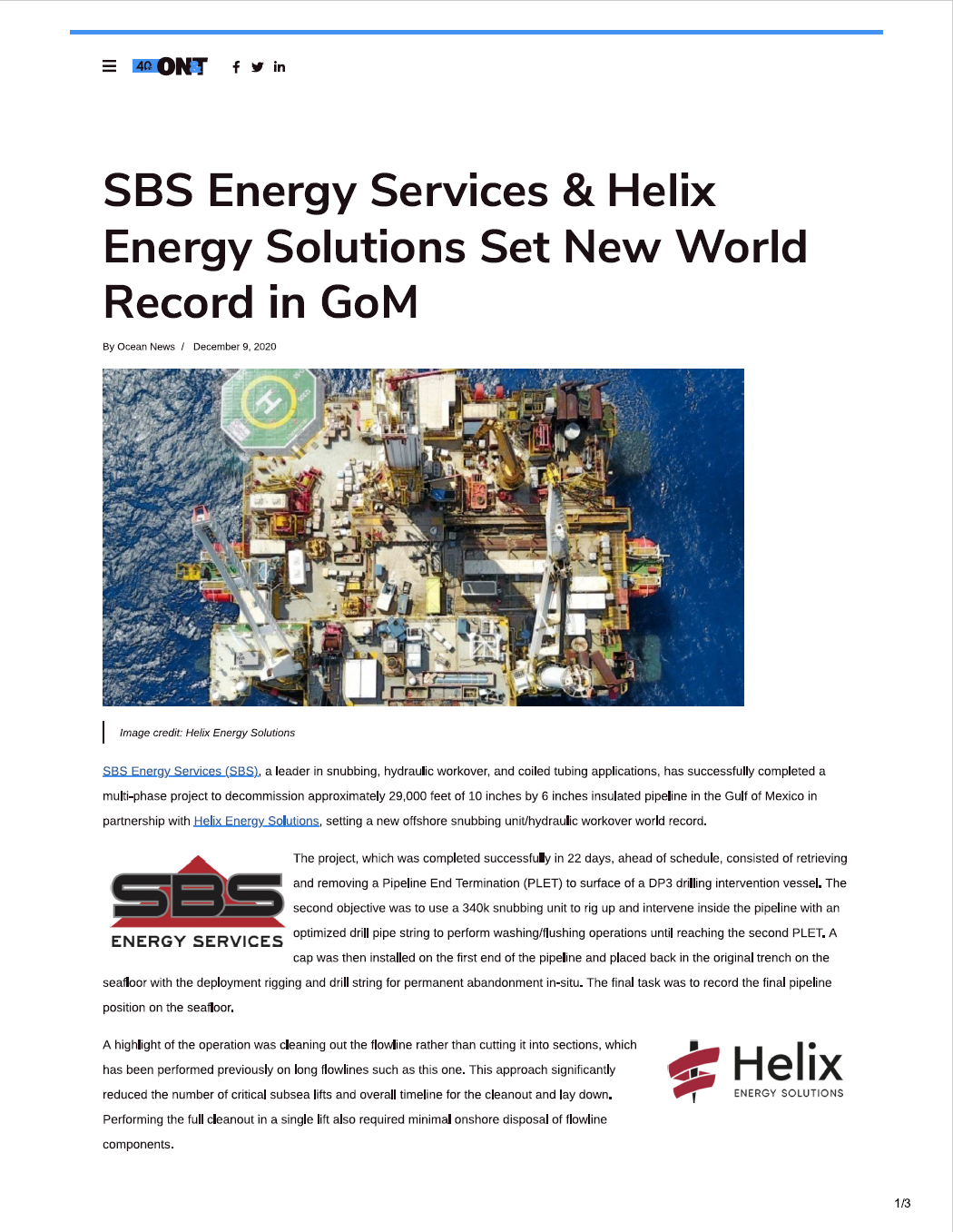
SBS Energy Services (SBS), a leader in snubbing, hydraulic workover, and coiled tubing applications, has successfully completed a multi-phase project to decommission approximately 29,000 feet of 10 inches by 6 inches insulated pipeline in the Gulf of Mexico in partnership with Helix Energy Solutions, setting a new offshore snubbing unit/hydraulic workover world record.
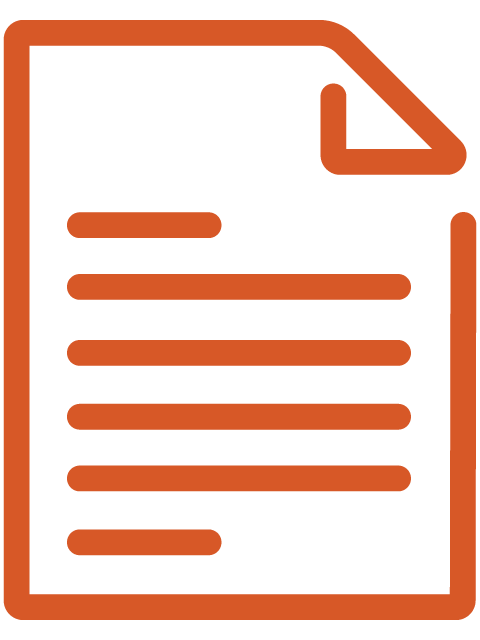
Abstract
A dynamic finite element analysis (FEA) calculation engine has been developed and is being used to solve specialized well intervention problems. This paper summarizes the theory used in this engine, and documents two of its applications. The first application is modeling the buckling behavior of pipe (or a bottom hole assembly) being snubbed through a packer. The second application is wireline being run from a boat to a subsea well to perform an intervention. The first step in this intervention is to jar the plug out of the tree.
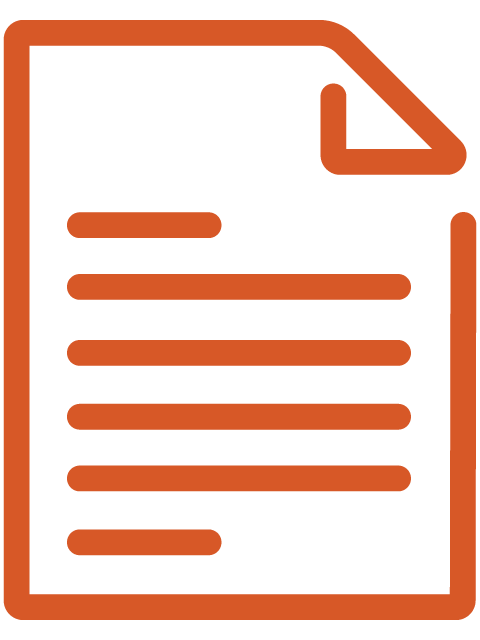
Abstract
Drilling productive reservoirs in near-depleted conditions is becoming more common. This operation is usually difficult
and troublesome. This paper describes a successful field case history whereby casing was set on top of a depleted zone and
nitrogen, coiled tubing, and a vane motor were used to drill underbalanced through the pay zone.
The reservoir had a bottomhole pressure of 150- to 200 psi at 5,000 ft. The reservoir would not withstand a column of
foam for circulation, and also water-based drilling fluids and foam would cause formation damage. The decision was made
to drill the section with coiled tubing and nitrogen. This type of operation required the use of a downhole motor that would
allow the use of a compressed gas as the power medium. The operation was successful.
This paper will discuss the following issues related to this operation: (1) existing field conditions, (2) objectives, (3) options considered, (4) modeling parameters, (5) equipment design parameters, (6) bit selection, (7) operations planning, (8) actual operations, (9) cost analysis, and (10) recommendations for future improvements.
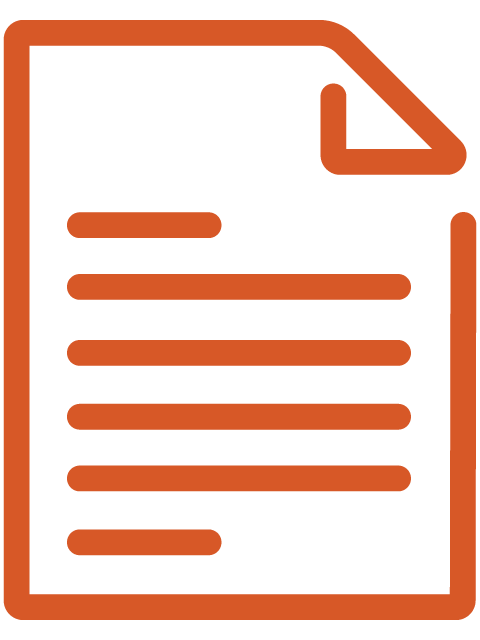
Abstract
This paper reviews the design, implementation, and results of a 22, 611 ft underbalanced coiled tubing scale
cleanout project for the wellbore of the Fort Stockton Gas Unit 5-1. The Fort Stockton Gas Unit 5-1 is a deep, low pressure, high temperature, Gomez (Ellenburger) Field gas well.